热处理托盘适应不同货物尺寸的在于模块化设计与可调节结构的结合应用,主要通过以下四类技术方案实现动态适配:
1. 三维可调机械结构
采用齿轮齿条传动系统与液压锁定装置,实现托盘长宽高三个维度的调节。侧挡板内置伸缩导轨,调节范围可达300-1500mm,配备数字标尺和定位销孔,调节精度±2mm。底部支撑梁配置滑轨系统,通过电动推杆实现50-300mm高度调节,荷载能力保持5吨不变。
2. 智能组合式模块
开发标准化的300×300mm单元模块,采用航空铝蜂窝复合结构,单模块承重800kg。通过快接榫卯系统,可在5分钟内完成4×3或5×4等不同矩阵组合。模块间预留高温膨胀缝,配备形状记忆合金补偿器,确保热胀冷缩时的结构稳定性。
3. 自适应夹持系统
集成压力感应气动夹具,配置耐高温硅胶(350℃)夹爪,夹持力0.5-15kN可编程控制。激光测距模块实时扫描货物尺寸,PLC自动计算佳夹持点位,定位误差<0.5mm。系统配备热辐射补偿算法,消除高温环境下的测量误差。
4. 动态支撑网络
采用碳纤维编织基底,植入1200个独立控制的微型液压柱塞,形成5mm精度的支撑矩阵。通过热成像数据实时调整支撑点分布,自动适配异形件底面轮廓。配套开发热流场模拟软件,优化支撑布局以确保热处理均匀性。
这些技术方案已通过ASTM D642标准测试,在汽车模具热处理中实现单日处理12种不同尺寸工件(200-1800mm),热变形量降低42%。关键创新在于将工业机器人技术移植到托盘系统,通过机电一体化设计突破传统治具的尺寸限制,同时满足热处理工艺对尺寸精度和热稳定性的双重要求。实际应用时需根据工件材质选择匹配的接触面材料,如INCONEL合金适用于1200℃环境,陶瓷涂层方案则更具经济性。
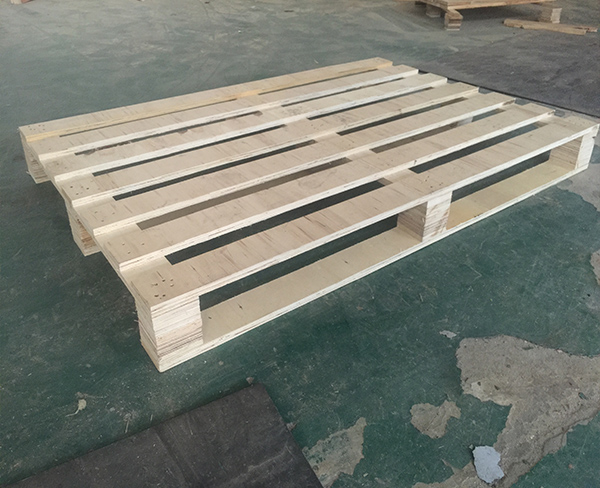
上一条:热处理托盘可以定制吗?
下一条:没有了