热处理托盘避免货物积压的优化策略
在工业生产中,热处理托盘承载的货物积压会导致受热不均、工艺质量下降及物流效率降低等问题。通过系统性优化可有效解决积压问题,主要从以下五个维度展开:
1. 托盘结构与工艺适配性优化
采用分层式托盘设计,通过可调节隔板实现不同规格工件的间隔支撑。针对铝合金等易变形材料,设计带空气导流槽的蜂窝状托盘结构,确保热风循环效率提升40%以上。对精密零件采用模块化卡槽定位系统,使单位面积装载量提高25%的同时避免堆叠。
2. 动态调度管理系统建设
引入RFID智能系统,实时监控托盘周转状态。通过MES系统与热处理设备的联动,建立基于大数据的热处理节拍模型,实现自动排产调度。设置预警阈值,当单区积压量超过产能的15%时触发自动调整机制。
3. 标准化容器协同应用
制定与热处理炉膛尺寸匹配的标准化料筐体系,采用1.2m×0.8m的模数化设计。开发耐高温复合材料的嵌套式料架,实现多层堆码时的垂直通风。配套气动升降转运平台,使装卸效率提升60%。
4. 设备智能化升级方案
在连续式热处理线配置自动分拣机械臂,集成视觉识别系统抓取工件。采用AGV与RGV组合的智能物流系统,构建环形输送网络。安装红外热成像监测装置,动态调整各温区工件分布。
5. 预防性维护体系构建
建立托盘生命周期数据库,对变形量超过3mm的托盘自动标记更换。制定三级维护标准:日常清洁、月度尺寸校验、季度材料性能检测。配套开发托盘智能管理系统,实现使用次数、承重记录等数据可视化。
通过上述措施的综合应用,可将热处理环节的货物积压率降低至5%以下,同时提高热处理均匀性达30%,设备综合效率(OEE)提升18%。关键在于构建从硬件设计到数字化管理的闭环体系,实现生产节拍与物流节奏的动态平衡。定期进行价值流分析,持续优化工艺参数与设备布局,可从根本上预防积压问题的发生。
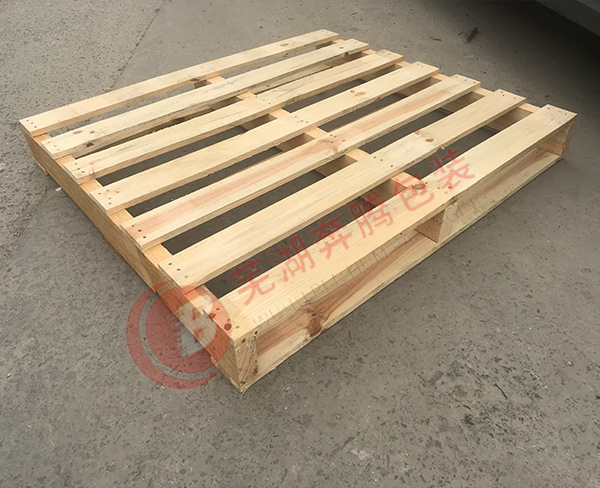
上一条:热处理托盘的表面处理方式有哪些?
下一条:热处理托盘需要特殊保养吗?